In 1974 Bendix introduced a hydraulic power brake booster patented under then name "Hydro-Boost"
(Figure 1).
Hydro-Boost features:
- Higher pressure available
- Stored energy reserve for power-off brake applications
- Lower power-off pedal efforts with pressure reserve depleted
- Smaller size
- Faster response time
- Vacuum source not required
The Hydro-Boost, in certain applications, has many advantages over vacuum boosters. It's compact
size allows it to be installed where underhood space is at a premium as with vans and compact cars.
A vacuum source is not necessary so the unit can be used on diesel powered cars or trucks and
turbocharged gasoline engines. lastly, because it's available boost is much higher than vacuum
units, it can be used in applications where greater master cylinder pressures are required. Light
to medium duty trucks and cars equipped with 4-wheel disc brakes are good examples. In all cases,
the brake system remains totally conventional because the Hydro-Boost simply mounts in place of
the normal vacuum booster. Figure 2 illustrates the schematic of the Hydro-Boost and its
relationship to the power steering pump.
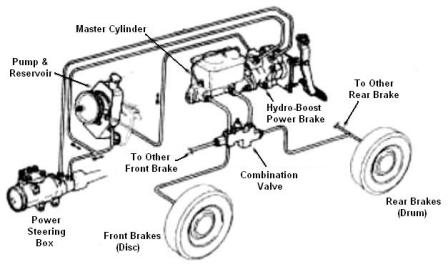
Figure 2
A sliding spool valve in the Hydro-Boost controls fluid flow from the power steering pump under
all operating conditions. During brake application the flow to the power steering gear remains
constant and the spool valve diverts fluid under pressure to the boost cavity of the Hydro-Boost.
Because of the spool valve action, the power brake unit and power steering unit do not interfere
with one another whether at rest or in use.
Three lines are connected to the power section. One of line directs pressure from the power
steering pump to the Hydro-Boost. A second line connects to the steering gear. The third is a
return line back to the steering pump reservoir. A fourth line would be used in conjunction with
a remote accumulator.
Should normal steering pump pressure be interrupted (i.e. stalled engine, ruptured steering hose,
or broken pump drive belt) a reserve pressure system will be activated.
The reserve system of an accumulator, check valve assembly, and a dump valve assembly
Three styles of accumulators have evolved since the introduction of the Hydro-Boost. A spring
loaded design (Figures 3 and 4) was used from 1974 - 1978. In 1981 the Hydro-Boost II system was
introduced which incorporated the accumulator into the power piston assembly. This made the assembly
more compact and lighter.
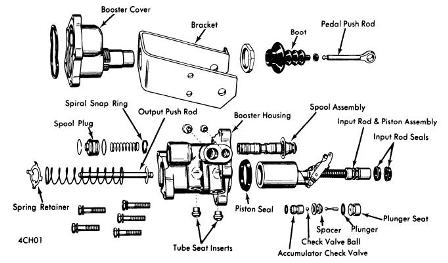
Figure 3
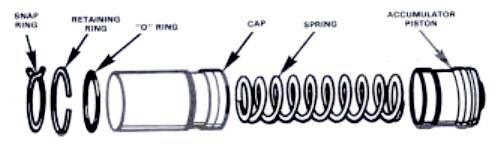
Figure 4
|